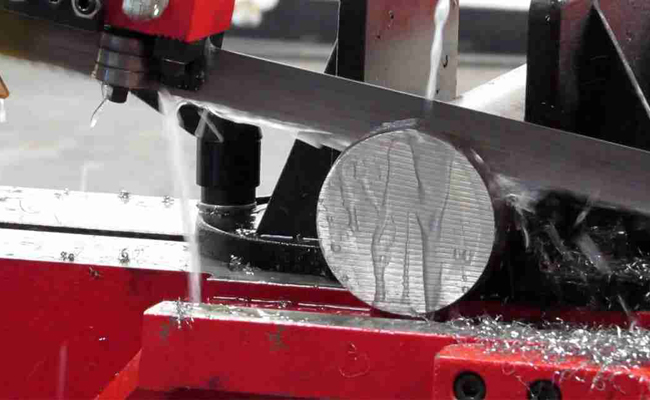
Poor Band Saw Cutting Performance? Choosing the Right Blade and Usage is Key!
Poor cutting performance on a band saw (e.g., rough cuts, deviation, frequent blade breakage) is often directly related to incorrect blade selection or improper operating parameters. Below is a systematic solution to quickly improve cutting quality.
I. Key Points in Blade Selection
1. Tooth Selection – Based on Material Type and Thickness
Regular Tooth:
Suitable for ductile materials like mild steel, aluminum, and copper. Recommended pitch: 6–10 TPI (teeth per inch).
Hook Tooth:
Ideal for fast cutting of wood, plastic, and soft metals. Large gullet (3–6 TPI) for efficient chip removal.
Variable Pitch:
Reduces vibration, best for thin-walled tubes and stainless steel. Recommended 8/12 TPI combination.
Material Thickness Matching Rule:
At least 3 teeth in contact with the workpiece. For example, when cutting 20mm-thick steel, choose at least 6 TPI (25.4 ÷ 6 ≈ 4.2mm/tooth).
2. Blade Material – Matching Material Hardness
Carbon Steel Blade:
Economical, suitable for soft metals (aluminum, mild steel), but shorter lifespan.
Bi-Metal Blade (M42/M51):
High-speed steel teeth + spring steel backing, versatile, ideal for stainless steel/alloy steel (5–8x longer lifespan).
Carbide-Tipped Blade:
For high-hardness materials (titanium alloy, hardened steel), excellent wear resistance but costly.
3. Blade Width – Affects Cutting Stability
Narrow Blade (6–10mm):
Best for small-radius curved cuts (e.g., radius ≥15mm).
Wide Blade (27–34mm):
Preferred for straight cuts, higher rigidity, reduces deviation.
II. Critical Operating Parameter Adjustments
1. Blade Speed (m/min)
Material Type | Recommended Speed Range |
---|---|
Aluminum | 300–600 |
Mild Steel | 40–80 |
Stainless Steel (Austenitic) | 20–40 |
Titanium Alloy | 10–30 |
Note: Excessive speed causes overheating; too low reduces efficiency.
2. Feed Pressure Control
Too Low: Blade slips, excessive wear on cut surface.
Too High: Tooth chipping, stepped cut surface.
Indicator: Chips should be tight spirals (steel) or continuous curls (aluminum). Powdery chips indicate insufficient pressure.
3. Cooling/Lubrication Optimization
Emulsion: General-purpose metal cutting (5%–10% concentration).
Oil-Based Coolant: Efficient cooling for stainless steel/titanium.
Dry Cutting: Only for aluminum or cast iron (reduce speed by 30%).
III. Common Problems & Solutions
1. Rough Cut Surface with Burrs
Cause: Too coarse tooth pitch, excessive feed, or worn blade.
Solution: Switch to a finer blade (e.g., 10 TPI), reduce feed pressure by 20%.
2. Frequent Blade Breakage
Checks:
Blade tension (typically 250–300 MPa).
Guide block wear (gap should be <0.05mm).
Workpiece clamping (vibration causes tooth breakage).
3. Cutting Angle Deviation
Calibration Steps:
Verify saw frame squareness with a right-angle gauge.
Adjust guide arm parallelism to blade (error ≤0.1mm/m).
Check if blade weld is smooth.
IV. Maintenance & Lifespan Extension Tips
New Blade Break-In:
Reduce speed/pressure by 30% for the first use. After cutting 50cm², resume full load.
Regular Cleaning:
Remove chips from tooth gullets (prevents secondary friction).
Tension Release:
Loosen blade if idle for >8 hours to prevent fatigue.