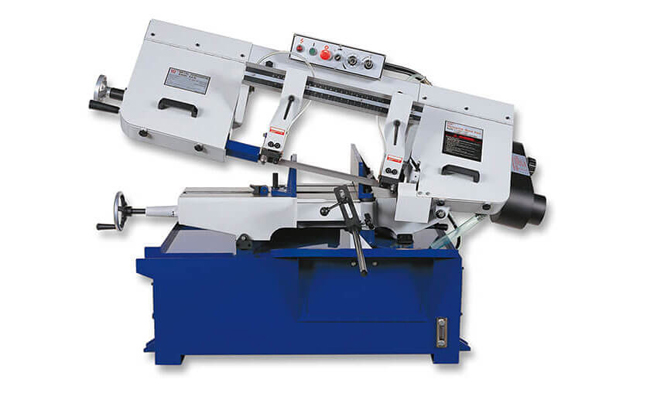
Why Your Band Saw Keeps Failing (And How to Fix It)
Frequent band saw malfunctions are usually caused by a variety of factors, including improper operation, lack of maintenance, or worn-out components. Below are common issues and their corresponding solutions to help you systematically troubleshoot the problem.
I. Common Causes and Solutions
1. Blade Breakage or Excessive Wear
Causes:
Incorrect blade tension (too tight or too loose).
Mismatched blade for the material (e.g., wrong tooth pitch).
Cutting too fast or uneven feed pressure.
Misaligned blade or guide wheels.
Fixes:
Adjust tension to the manufacturer’s recommended setting (typically ~6mm side deflection when pressed).
Select the right tooth pitch (fine teeth for thin materials, coarse for thick).
Reduce cutting speed and maintain consistent feed pressure.
Check blade alignment and adjust guide bearings.
2. Crooked Cuts or Material Drifting
Causes:
Dull or damaged blade teeth.
Worn or improperly adjusted guide bearings.
Misaligned table or fence.
Fixes:
Replace the blade or file damaged teeth (if minor).
Adjust guide bearings (0.1–0.3mm gap) and ensure they spin freely.
Use a square to check table and fence alignment (90° perpendicular).
3. Excessive Noise or Vibration
Causes:
Loose blade or worn wheel bearings.
Unstable machine base or uneven flooring.
Worn drive belt or misaligned motor shaft.
Fixes:
Re-tension the blade; replace faulty bearings (check for rough rotation).
Stabilize the base, level the floor, or add anti-vibration pads.
Inspect belt tension, replace cracked belts, and realign the motor shaft.
4. Blade Keeps Slipping Off
Causes:
Worn tires or undersized wheels reducing grip.
Faulty tension spring.
Poorly welded blade joint (for joined blades).
Fixes:
Replace worn tires (common with rubber deterioration).
Replace or adjust the tension spring.
Reweld the blade smoothly or switch to a continuous blade.
5. Motor Overheating or Shutting Off
Causes:
Overloading (hard material or dull blade).
Poor ventilation or voltage fluctuations.
Failed capacitor (common in single-phase motors).
Fixes:
Reduce feed rate; use a sharper blade.
Clean motor vents; check voltage stability (±10% of rated value).
Test capacitor with a multimeter and replace if faulty.
II. Preventive Maintenance Tips
Daily Care:
Clean sawdust (especially around guides and bearings) after each use.
Lubricate bearings and moving parts (light oil or lithium grease).
Release blade tension when not in use to reduce fatigue.
Regular Checks:
Monthly: Verify table and fence squareness.
Biannually: Replace drive belts (adjust based on usage).
Annually: Inspect motor brushes (if applicable) and wiring insulation.
Best Practices:
Let the blade cut naturally—avoid forcing material.
Use dedicated blades for different materials (metal, wood, plastic).
Allow a 10-second idle run before cutting to check for abnormalities.
III. Recommended Tools & Spare Parts
Essential Tools: Tension gauge, square, feeler gauge (for gaps), bearing puller.
Common Consumables: Spare blades (various pitches), guide bearings, belts, grease.
Following these steps can resolve over 80% of band saw issues. If problems persist, structural damage or electrical faults may be the cause—consult a professional. Regular maintenance and proper operation significantly extend tool life!