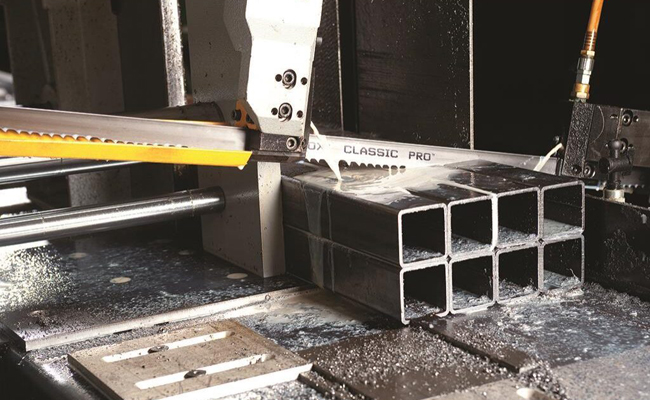
How to scientifically evaluate the performance and durability of band saws: from key indicators to actual combat tests
As the core equipment of modern processing industry, the performance and durability of band saws directly affect production efficiency and processing quality. To comprehensively evaluate the comprehensive quality of a band saw, it is necessary to conduct a systematic analysis from the following key dimensions:
1. Core performance indicator evaluation system
Cutting accuracy detection
Straight-line cutting test: Use a dial indicator to measure the straightness deviation of a 3-meter-long workpiece after cutting. High-quality equipment should be controlled within 0.15mm/m
Repeat positioning accuracy: Cut at the same position 10 times in a row to measure the size fluctuation range. Industrial-grade equipment should be ≤±0.05mm
Bevel angle accuracy: When testing 45° bevel cutting, the angle deviation should not exceed ±0.5°
Power system efficiency
Main motor torque curve: Use a power analyzer to detect the torque output stability under different loads. The fluctuation range of high-quality motors should be <5%
Speed ??change performance test: The speed change time from the lowest to the highest speed should be ≤3 seconds (higher requirements for metal cutting models)
Energy efficiency ratio: Measure the energy consumption per unit material cutting. The higher the energy efficiency ratio, the better the performance of similar equipment
Cutting efficiency parameters
Feed speed adjustment range: Wood cutting should reach 5-50m/min, metal cutting 0.5-15m/min
Maximum cutting capacity: Compare with standard The measured value and the actual cutting test results, high-quality equipment should have a safety margin of more than 15%
Adaptability to different materials: Test the cutting performance from softwood to hardwood, or from aluminum alloy to stainless steel
2. Key verification factors for durability
Verification of structural durability
Frame vibration test: Use a vibration analyzer to detect under maximum load, the amplitude should be <0.02mm
Guide rail wear test: After 200 hours of continuous operation, use a three-coordinate measuring instrument to detect the change in guide rail straightness
Material of key components: The spindle should use GCr15 bearing steel, and the guide rail should use at least HT250 cast iron
Transmission system reliability
Gearbox temperature rise test: The oil temperature should not exceed 65℃ after continuous operation for 8 hours
Belt/chain life: The service life should be guaranteed to be more than 3000 hours under standard load
Bearing durability: Only ABEC-5 and above bearings can meet industrial-grade requirements
Life assessment of wearing parts
Saw blade life: High-quality bimetallic saw blade When cutting ordinary steel, effective cutting should be maintained for more than 50 hours
Guide block wear cycle: Tungsten steel guide blocks should maintain a working life of 800 hours under normal use
Cooling system durability: The pump body should ensure 5000 hours of trouble-free operation
3. Actual combat test method
Step load test method
Use progressive load test: Starting from 30% rated load, increase the load by 10% every 2 hours until 120% rated load, and observe the equipment status change curve
Continuous endurance test
Continuous operation for 72 hours (simulating three-shift production), record the drift of key parameters
Extreme working condition simulation
Low temperature start test: cold start performance under -10℃ environment
High humidity test: continuous working test under 85% humidity environment
Voltage fluctuation test: operation stability under ±15% voltage fluctuation
4. New dimension of intelligent evaluation
Status monitoring system
Real-time vibration analysis capability
Temperature abnormal warning accuracy
Load fluctuation Monitoring sensitivity
Predictive maintenance function
Wear trend prediction accuracy
Remaining life estimation error range
Fault warning response time
Adaptive control performance
Material identification accuracy
Parameter automatic adjustment response speed
Abnormal cutting state self-correction ability
V. Purchase decision reference framework
Cost-performance evaluation model
Total equipment cost = purchase cost + 5-year maintenance cost + energy consumption cost – residual value
Brand technology reserve
Patent quantity and quality
Core component self-production rate
Technology iteration cycle
Service network evaluation
After-sales service response time
Technical support capability
Spare parts supply guarantee
It is recommended to require suppliers to provide the following before purchasing:
Third-party test report (such as TüV, SGS)
Actual user case report
Material certification of key components
Through this systematic evaluation system, users can not only accurately judge the immediate performance of the band saw machine, but also scientifically predict its long-term use value, providing a comprehensive and objective decision-making basis for equipment selection. In the actual evaluation process, it is recommended to combine your own production needs to conduct a weighted evaluation of key indicators to ensure the selection of the most suitable equipment solution.