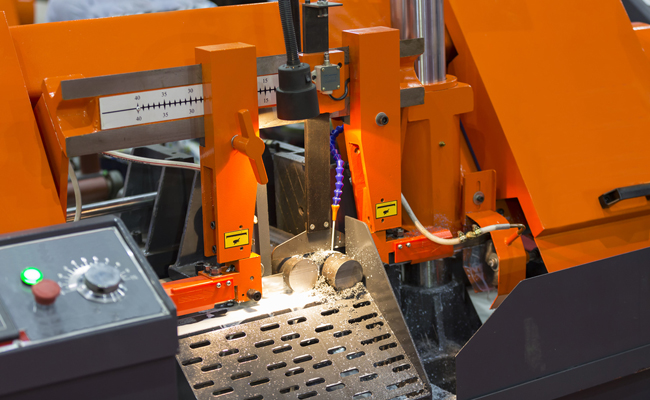
How a Metal Band Saw Works: Core Principles of Efficient Metal Cutting Explained in 3 Minutes
In metalworking, metal band saws are the go-to equipment for cutting pipes, profiles, and alloy components due to their high efficiency and low material waste. Yet, many users lack a clear understanding of their working principles. This article breaks down the core mechanisms, workflow, and advantages of metal band saws in simple terms, helping you master this essential technology quickly!
1. Core Principles of Metal Band Saws
A metal band saw uses a high-speed continuous band blade with hardened teeth to “scrape” or “shear” through metal, gradually separating the workpiece. It exemplifies linear cutting technology, offering narrow kerfs (1-2mm) and minimal material loss compared to traditional circular saws or grinding wheels.
Key Principles Explained:
Power Transmission: A motor drives the main wheel, rotating the band blade at speeds up to 1,000 meters per minute.
Tooth Cutting Action: Hardened teeth (e.g., high-speed steel or tungsten carbide) remove material layer by layer.
Continuous Feed: Hydraulic or gravity systems control downward pressure to ensure stable cutting.
2. 5 Essential Components of a Metal Band Saw
Understanding its structure is key to grasping how it works:
Component | Function |
---|---|
Band Blade | A toothed looped blade; material varies (e.g., tungsten carbide for hard metals). |
Drive Wheel & Idler Wheel | The drive wheel powers the blade; the idler wheel maintains tension. |
Guide System | Uses bearings or blocks to stabilize the blade, ensuring precision (critical for thick materials). |
Cooling System | Sprays coolant to reduce heat, lubricate, and flush away metal chips. |
Workpiece Clamping Table | Secures materials during cutting (manual/hydraulic clamping options). |
3. Step-by-Step Workflow (Visual Guide)
Step 1: Startup & Speed Adjustment
Set blade speed based on material hardness (e.g., high speed for aluminum, low speed for stainless steel).
Step 2: Secure the Workpiece
Clamp the material onto the table and adjust cutting angles (supports 0°–60° bevel cuts).
Step 3: Begin Cutting
The blade moves continuously while hydraulic pressure ensures steady penetration until the cut is complete.
Step 4: Coolant & Chip Removal
Coolant is sprayed to lower temperatures and clear chips, preventing blade clogging.
4. 4 Key Advantages & Applications
Advantages
High Efficiency: 1-2mm kerf width maximizes material use (up to 99% efficiency).
Energy Savings: Consumes 30% less power than traditional cutting tools.
Versatility: Cuts round, irregular shapes (e.g., H-beams, titanium tubes).
Automation Compatibility: Integrates with CNC systems for mass production.
Industries
Metal Fabrication: Cutting profiles, bars, and rods.
Automotive Manufacturing: Processing drive shafts, gear blanks.
Aerospace: Precision cutting of aluminum/titanium components.
5. Frequently Asked Questions (FAQ)
Q1: What’s the maximum thickness a band saw can cut?
A: Standard machines handle ≤300mm; heavy-duty models cut up to 600mm.
Q2: How to extend blade life?
A: ① Match tooth pitch (TPI) to material thickness; ② Check tension regularly; ③ Use coolant consistently.
Q3: Why do blades break when cutting stainless steel?
A: Stainless steel’s hardness and poor heat conductivity require slower speeds and carbide-tipped blades.
Mastering how a metal band saw works improves cutting efficiency and reduces maintenance costs. Whether purchasing equipment or training operators, understanding its principles is vital. For more insights on band saw selection or cutting parameter optimization, stay tuned for our upcoming guides!