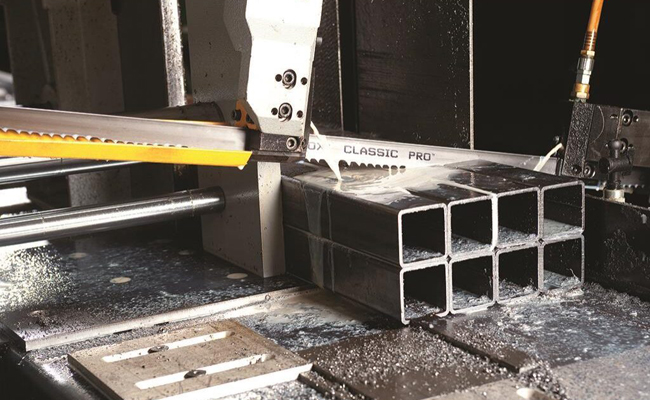
How to Choose a Horizontal Bandsaw for Maximum Productivity
In industries such as metalworking and wood manufacturing, horizontal bandsaws are essential for efficient cutting. Selecting the right bandsaw not only improves productivity but also reduces operational costs and extends equipment lifespan. This article systematically analyzes how to choose a horizontal bandsaw for maximum productivity, covering equipment selection, performance parameters, blade matching, automation level, and maintenance management.
1. Define Production Requirements
1.1 Material Type
Different materials have varying requirements:
Metal cutting (steel, aluminum, alloys): Requires high power, wear-resistant blades, and stable feed systems.
Wood processing: Focuses on high cutting speed, low vibration, and surface finish.
Composites/plastics: Needs anti-clogging tooth design to prevent material buildup.
1.2 Material Dimensions
Maximum cutting size (height × width): Determines throat depth and stroke.
Minimum cutting thickness: Affects blade tooth pitch (fine teeth for thin materials, coarse teeth for thick materials).
Batch production needs: Determines whether an automatic feeding system is required.
1.3 Production Cycle Requirements
Single-piece cutting time: Influences manual vs. semi-automatic vs. fully automatic selection.
Material change frequency: High-frequency changes require quick clamping systems.
2. Key Performance Parameters
2.1 Power System
Application | Recommended Motor Power | Drive System |
---|---|---|
Small wood/aluminum cuts | 5-10 HP | Mechanical/belt drive |
Medium steel cutting | 15-25 HP | Hydraulic/servo drive |
Heavy-duty industrial | 30 HP+ | Variable frequency + servo control |
2.2 Cutting Accuracy
Straightness error: ≤0.1mm/m for high precision (e.g., aerospace).
Angular cutting accuracy: Within ±0.5°.
Surface roughness: Ra≤3.2µm for metal, Ra≤6.3µm for wood.
2.3 Automation Level
Automation Grade | Application | Typical Configuration |
---|---|---|
Manual | Small batch, multi-variety | Manual clamping & feeding |
Semi-automatic | Medium batch production | Hydraulic clamping, auto feeding |
Full-auto CNC | Mass production, high precision | Robotic loading, auto-measurement |
3. Blade Selection & Matching
3.1 Blade Material
Blade Type | Suitable Materials | Characteristics |
---|---|---|
Carbon steel blade | Softwood, plastics | Low cost, shorter lifespan |
Bi-metal blade | Steel, aluminum | High wear resistance, cost-effective |
Carbide-tipped blade | Titanium, stainless steel | Ultra-long lifespan, ideal for hard materials |
3.2 Tooth Parameters
Material Thickness | Recommended TPI | Tooth Type | Cutting Speed (m/min) |
---|---|---|---|
<5mm | 18-24 TPI | Fine teeth | 80-120 |
5-50mm | 10-14 TPI | Standard alternate | 60-80 |
>50mm | 6-8 TPI | Coarse pitch | 40-60 |
4. Structural Design & Durability
4.1 Machine Structure
Frame type: Solid cast iron (better vibration damping) over welded structure.
Guide system: Linear guides (high precision) vs. roller guides (high load).
Wheel balancing: Dynamically balanced wheels reduce vibration and extend blade life.
4.2 Key Components
Hydraulic system: Stable pressure control prevents blade breakage.
Guide blocks: Carbide guides minimize blade wear.
Cooling system: Forced cooling for metal, chip removal for wood.
5. Productivity Optimization Strategies
5.1 Cutting Parameter Optimization
Material | Speed (m/min) | Feed Pressure (kg) | Cooling Method |
---|---|---|---|
Aluminum | 100-150 | 20-30 | Emulsion cooling |
Steel | 60-90 | 30-50 | Oil-based cooling |
Hardwood | 80-120 | 15-25 | Air cooling/dry cutting |
5.2 Production Process Optimization
Gang cutting: Multiple pieces in one pass to reduce idle time.
Auto-feeding: Minimizes manual intervention for continuous operation.
Preventive maintenance: Regular lubrication and blade tension calibration.
6. Brand & Cost-Effectiveness Recommendations
Brand | Features | Best For |
---|---|---|
Amada | High precision, durability | High-end metalworking |
Kasto | German engineering, stability | Heavy-duty industrial |
DoAll | High automation | Mass production |
Local premium | Cost-effective, easy maintenance | SMEs, wood processing |
7. ROI Analysis
Initial cost vs. long-term benefits:
Fully automatic saws have higher upfront costs but reduce labor by 30%+.
High-quality blades cost more but last 50% longer, reducing replacement frequency.
Downtime cost: Reliable brands minimize unplanned stoppages.
Choosing a horizontal bandsaw requires balancing material properties, production needs, machine performance, blade matching, and automation. Maximum productivity = right equipment + optimized parameters + proper management. Recommendations:
Test cuts: Verify performance with actual materials before purchase.
Maintenance plan: Prevent efficiency loss due to poor upkeep.
Operator training: Proper usage maximizes equipment potential.
With the right selection and optimization, a horizontal bandsaw can become a core asset for boosting production efficiency.