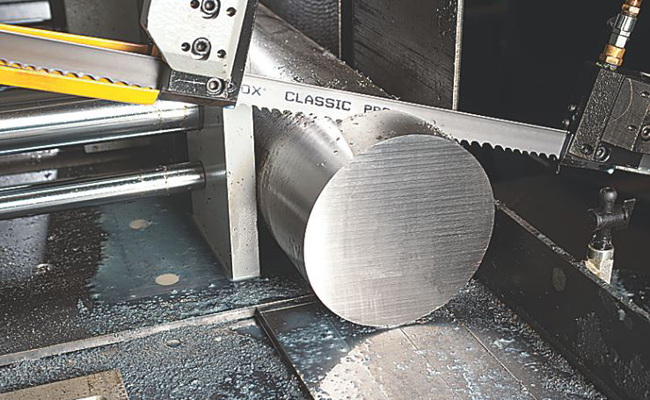
Comprehensive Guide to Band Saw Cutting: Principles, Material Selection, and Operation Techniques
Band saws are essential equipment in modern metalworking and non-metal cutting, widely used in industries such as machinery manufacturing, construction, automotive, and aerospace. Their high efficiency and precision make them a core machine in workshops. However, different materials have distinct physical properties, and selecting the right blade, adjusting parameters, and troubleshooting common issues directly impact processing efficiency and product quality. This guide systematically explains band saw cutting principles, material characteristics, blade selection, parameter optimization, and maintenance to help operators improve cutting quality and extend equipment lifespan.
1. Working Principle and Structure of Band Saws
Band saws use a motor to drive two wheels that rotate a continuous loop blade at high speed, enabling continuous cutting of workpieces. Key components include:
Frame: Supports the entire machine, ensuring stability.
Wheels: Drive the blade, with the upper wheel typically adjustable for tension.
Blade Tensioning Device: Maintains proper blade tension to prevent slipping or breakage.
Blade Guide System: Ensures smooth blade movement and reduces vibration.
Workpiece Clamping Device: Secures the workpiece to prevent shifting during cutting.
Cooling System: Reduces cutting temperature and extends blade life.
Band saws can be classified as vertical (for precision cutting) or horizontal (for high-volume long-material cutting).
2. Cutting Characteristics of Common Materials
1. Metal Materials
(1) Ferrous Metals
Carbon Steel (Low, Medium, High Carbon)
Properties: Moderate hardness, easy to cut, but high-carbon steel requires slower speeds.
Common Issues: Chip adhesion, faster blade wear.
Alloy Steel (Tool Steel, Mold Steel, Stainless Steel)
Properties: High hardness, especially chromium/molybdenum stainless steel, prone to work hardening.
Common Issues: Blade dulling; requires wear-resistant blades.
Cast Iron (Gray Iron, Ductile Iron)
Properties: Brittle, produces powdery chips.
Common Issues: Rapid tooth wear; requires enhanced cooling.
(2) Non-Ferrous Metals
Aluminum & Alloys
Properties: Soft, low cutting resistance, but prone to sticking.
Common Issues: Chip clogging; requires coarse-pitch blades.
Copper & Alloys
Properties: High ductility, produces long chips.
Common Issues: Chip entanglement; requires sharp teeth.
Titanium Alloys
Properties: High strength, poor thermal conductivity, generates high heat.
Common Issues: Short blade life; requires coated blades and ample cooling.
2. Non-Metal Materials
Plastics (PVC, PE, PP, etc.)
Properties: Soft, melts easily; requires low cutting speeds.
Common Issues: Melting and sticking to the blade.
Rubber
Properties: Elastic, causes blade vibration.
Common Issues: Uneven cuts; requires high-tension blades.
Wood
Properties: Fibrous structure, low cutting resistance.
Common Issues: Sawdust clogging; requires coarse-pitch blades.
3. Blade Selection and Optimization
1. Tooth Profile Selection
Regular Tooth: General-purpose, suitable for most steels.
Hook Tooth: High chip removal, ideal for soft materials like aluminum and plastics.
Precision Tooth: Fine cuts, best for thin-walled tubes and high-precision work.
2. Tooth Pitch Selection
Soft Materials (Aluminum, Plastics): 4/6 TPI (large pitch for chip clearance).
Medium-Hard Materials (Carbon Steel, Copper): 8/10 TPI (balanced cutting and chip removal).
Hard Materials (Stainless Steel, Titanium): 10/14 TPI (small pitch to reduce tooth chipping).
3. Blade Material
Carbon Steel Blades: Economical, for general steel, shorter lifespan.
Bi-Metal Blades (HSS teeth + spring steel back): Durable, for stainless steel and alloy steel.
Carbide-Tipped Blades: For ultra-hard materials (e.g., hardened steel, titanium).
4. Cutting Parameter Optimization
Material | Cutting Speed (m/min) | Feed Pressure | Cooling Method |
---|---|---|---|
Low-Carbon Steel | 30-60 | Medium-High | Water-soluble coolant |
Stainless Steel | 15-30 | Low | Oil-based coolant |
Aluminum | 100-300 | High | Air blast/special coolant |
Titanium | 10-20 | Very Low | High-flow coolant |
Plastics | 50-100 | Low | Dry cut/air cooling |
Key Adjustment Principles:
Hard Materials: Low speed, low feed, ample cooling.
Soft Materials: High speed, high feed, focus on chip removal.
5. Common Issues and Solutions
1. Blade Breakage
Causes: Excessive tension, worn guides, high feed pressure.
Solution: Adjust tension (300-400 N/mm² recommended), replace guides, reduce feed.
2. Rough Cuts
Causes: Incorrect tooth pitch, worn blade, excessive feed.
Solution: Use proper blade, reduce feed, check guides.
3. Cutting Deviation
Causes: Misaligned guides, unstable workpiece clamping.
Solution: Realign guides, secure workpiece firmly.
4. Short Blade Life
Causes: Improper parameters, insufficient cooling, hard material.
Solution: Optimize settings, increase cooling, upgrade blade quality.
6. Safety and Maintenance
1. Safety Guidelines
Wear PPE (safety glasses, gloves, ear protection).
Ensure workpiece is securely clamped.
Never adjust the machine while running.
Clear chips regularly to maintain cutting accuracy.
2. Maintenance Checklist
Daily: Check blade tension, guide wear, coolant level.
Weekly: Clean rails, lubricate moving parts.
Monthly: Inspect motor belts, replace worn guides.
Quarterly: Replace coolant, inspect electrical systems.
Efficient band saw operation depends not only on the machine itself but also on the operator’s understanding of material properties, blade selection, and parameter tuning. By choosing the right blade, optimizing settings, and performing regular maintenance, cutting quality can be significantly improved while extending equipment life and reducing costs. This guide aims to serve as a practical reference for maximizing band saw performance in industrial applications!