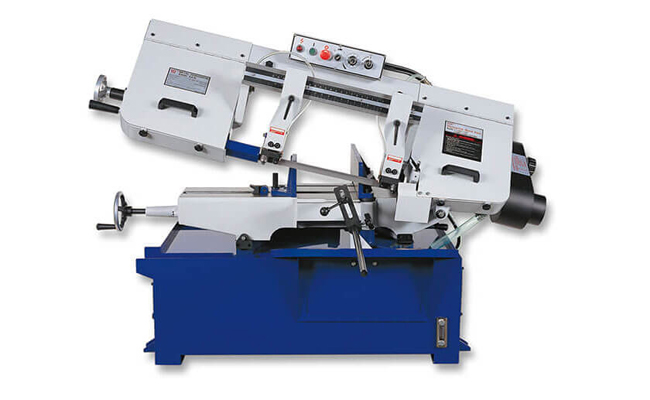
Manufacturer’s Guide on How to Address Workpiece Tapering During Band Saw Cutting
1. First, Check the Saw Blade
If the sawing machine previously worked normally and the blade was fine, but tapering occurs after replacing the blade, the issue is likely related to the saw blade quality.
Tooth Type Compatibility: Ensure the blade’s tooth pattern (e.g., regular, skip, or variable pitch) matches the material thickness and hardness (e.g., coarse teeth for thick materials, fine teeth for thin sheets).
Welding Quality: Check if the blade weld is smooth—excessive thickness or misalignment can cause vibration.
Material Suitability: Confirm the blade is appropriate for the workpiece (e.g., carbide-tipped blades for stainless steel, bi-metal for general steel).
Installation & Run-In
Tension Calibration: Use a tension gauge; recommended tension is typically 250–300 N/mm²—too loose causes slippage, too tight may break the blade.
Run-In Period: Reduce feed rate by 30% for the first 20 cuts to prevent premature wear-induced tapering.
2. Inspect the Saw Machine’s Mechanical Condition
If the blade is not the issue, check the machine’s alignment and components.
Guide System Adjustment
Guide Block Gap: Adjust to 0.05–0.1mm (use a feeler gauge) to avoid excessive friction.
Guide Arm Alignment: Ensure both arms are coaxial (deviation <0.2mm) to prevent blade twisting.
Coolant Flow: Verify coolant is directed at the teeth to prevent chip buildup and side pressure.
Saw Frame Perpendicularity
Vertical Alignment: Check with a square—error should be ≤0.1mm/300mm.
Horizontal Leveling: Adjust leveling feet to keep machine tilt <0.2mm/m.
Feed System Check
Hydraulic Pressure Test: Ensure feed cylinder pressure is 1.5–2.5 MPa (excessive pressure overloads the blade).
Servo Motor Feedback (CNC Models): Verify encoder stability to rule out irregular feed speed.
3. Optimize Cutting Parameters
Feed Rate Calculation:
Feed (mm/min) = Teeth Per Inch (TPI) × Chip Load (mm/tooth) × Cutting Speed (m/min)
Example: 3 TPI blade cutting mild steel (chip load 0.03mm/tooth, speed 20m/min) → Feed ≈ 1.8mm/min.
Speed Adjustment:
Hard materials (e.g., titanium): 15–25 m/min
Soft materials (e.g., aluminum): 50–80 m/min
4. Systematic Maintenance Plan
Critical Component Lifespan
Bearings: Replace spindle bearings every 3,000 hours or 2 years; check guide wheel bearings every 2,000 hours.
Hydraulic Oil Cleanliness: Maintain NAS 1638 Class ≤8; replace filters every 6 months.
Preventive Maintenance
Daily Checks: Lubricate rails (lithium grease), check belt tension (deflection <5mm).
Quarterly Maintenance: Test hydraulic seals, clean electrical cabinets.
5. Special Case Handling
Irregular-Shaped Workpieces: Use custom fixtures to align the center of gravity with the cutting line.
Thin-Wall Tubes: Add nylon sleeves to dampen vibration-induced tapering.
Following these steps resolves over 95% of tapering issues. If problems persist, use a laser interferometer for dynamic accuracy testing or contact the manufacturer for servo system recalibration.