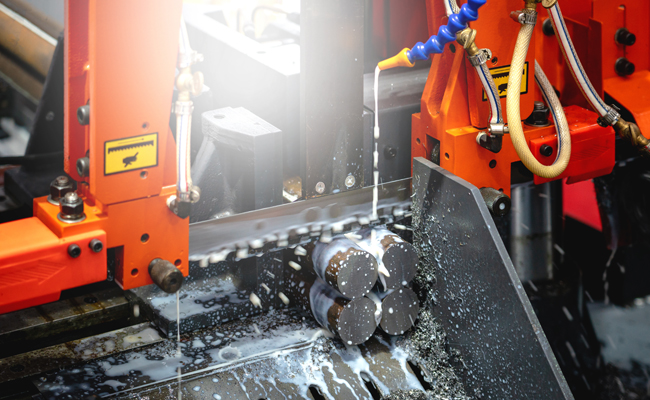
How to scientifically evaluate the performance and durability of band saws
As an important equipment in the fields of wood processing, metal cutting, etc., the performance and durability of band saws are directly related to production efficiency and processing quality. This article will systematically analyze the key indicators and methods for evaluating the performance and durability of band saws from a professional perspective, and provide a reference for equipment selection and maintenance.
1. Core indicators for band saw performance evaluation
1. Cutting efficiency and accuracy
Cutting efficiency is the primary indicator for measuring the performance of band saws, which is mainly reflected in:
Cutting speed: The cutting speed of high-quality band saws should remain stable and not be significantly affected by changes in material hardness
Feed rate: High-performance equipment can achieve precisely controlled variable speed feeding to meet the needs of different materials
Cutting accuracy: including straightness (usually required ≤0.1mm/100mm) and surface roughness (Ra value)
Professional advice: Use standard test blocks for cutting experiments, measure dimensional deviation and surface quality, and compare the manufacturer’s nominal parameters.
2. Power system performance
Motor performance: Inspect the rated power and actual output stability. The speed fluctuation of high-quality motors should be less than ±2% when the load changes
Transmission efficiency: The energy loss rate of the belt or gear transmission system should be less than 15%
Start-up characteristics: Record the time from startup to full speed operation. High-performance motors usually reach the operating speed within 3-5 seconds
3. Automation and ease of operation
The performance differences of modern band saws are also reflected in:
CNC system: evaluate programming flexibility, parameter storage capacity and human-computer interaction interface friendliness
Automatic feeding system: detect positioning accuracy (usually ±0.05mm) and repeat positioning accuracy
Safety protection: Emergency braking response time should be less than 0.5 seconds, and protective devices should comply with ISO 19085 standards
2. Six dimensions of durability evaluation
1. Material analysis of key components
Saw wheel: The life of high-quality cast iron or steel saw wheels can reach more than 3 times that of ordinary castings
Guide rail system: The wear resistance of quenched and hardened guide rails is 50-80% higher than that of ordinary guide rails
Bearings: The service life of brand bearings such as NSK or SKF is usually more than 10,000 hours
2. Structural design and manufacturing process
A band saw machine with good durability should have:
Integral casting frame: Compared with the welded structure, the vibration is reduced by more than 40%
Stress relief treatment: The deformation of the fuselage after aging treatment is less than 0.02mm/m
Anti-corrosion treatment: The electroplating or spraying process should be able to ensure that it will not rust for more than 5 years
3. Design for maintenance convenience
Lubrication system: The central automatic lubrication system can extend the maintenance interval to 500 hours
Replacement of wearing parts: The time for replacing the saw blade of a well-designed band saw machine should be controlled within 15 minutes
Maintenance channel: Key components should be able to be maintained without disassembling the entire machine
3. Actual test verification method
1. Laboratory standard test
Continuous load test: Run continuously for 72 hours at 110% of the rated load and record the performance degradation
Fatigue test: Simulate the actual working cycle. High-quality equipment should be able to withstand more than 500,000 cycles without obvious wear
Environmental adaptability test: Including temperature and humidity changes (-10℃ to 50℃) and vibration test (5-500Hz sweep frequency)
2. On-site working condition verification
It is recommended to conduct a 30-day production environment test:
Record the time between failures (MTBF): Industrial-grade equipment should reach more than 2000 hours
Measurement accuracy changes: Test key accuracy indicators once a week
Evaluate energy consumption ratio: Calculate the energy consumption cost per unit output
4. Purchase and maintenance recommendations
Cost-effectiveness evaluation: Do not simply compare prices, but calculate life cycle costs (including energy consumption, maintenance, downtime losses, etc.)
Scientific evaluation of the performance and durability of band saws requires a combination of quantitative indicators and actual verification. It is recommended that users conduct sufficient testing and comparison before purchasing, and establish a sound equipment management system. Although the initial investment of high-performance and high-durability band saw machines is relatively high, they can significantly reduce the processing cost of each piece and improve the stability of product quality in the long term. They are a wise choice for modern manufacturing industries to achieve efficient production.