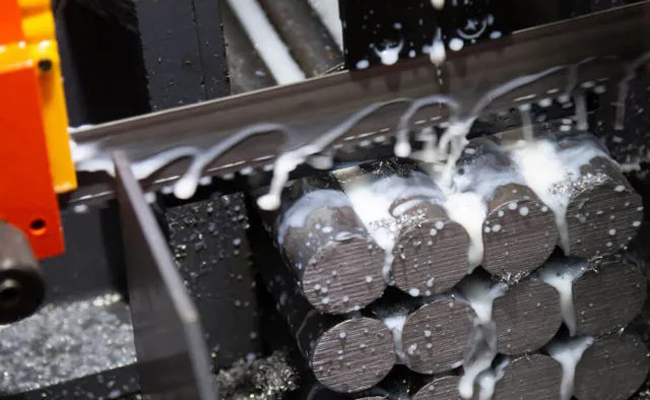
Analysis of Material Dimensional Accuracy Issues in CNC Sawing Machines
CNC sawing machines play a crucial role in metal processing, and their cutting accuracy directly impacts product quality and production efficiency. However, in practical use, inaccurate material dimensional accuracy is a common issue. This article will analyze the potential causes of this problem from the perspectives of equipment, process, operation, and environment, and provide corresponding solutions.
1. Equipment Issues
The performance and quality of the equipment itself are key factors affecting cutting accuracy.
Blade Issues:
Causes: Blade wear, mismatched tooth profiles, or improper installation can lead to cutting deviations.
Solutions: Regularly inspect the blade condition, replace severely worn blades promptly, ensure the blade type matches the material, and install it correctly.
Guide Rail and Transmission System Issues:
Causes: Wear on guide rails, insufficient lubrication, or loose transmission components (such as lead screws or belts) can cause unstable movement, affecting accuracy.
Solutions: Regularly maintain guide rails and transmission systems, ensure adequate lubrication, and check and tighten loose components.
Clamping Device Issues:
Causes: Insufficient clamping force or inaccurate clamping positions can cause material movement during cutting.
Solutions: Inspect the clamping device to ensure even and sufficient clamping force, and adjust the clamping position to secure the material.
CNC System Issues:
Causes: Incorrect parameter settings or system malfunctions in the CNC system may lead to inaccurate execution of cutting commands.
Solutions: Check CNC system parameters to ensure they meet processing requirements, and contact the supplier for system maintenance or upgrades if necessary.
2. Process Issues
Cutting process settings directly affect cutting accuracy.
Cutting Speed Issues:
Causes: Excessive or insufficient cutting speed can affect cutting quality, leading to dimensional deviations.
Solutions: Adjust cutting speed based on material type and thickness to ensure a stable cutting process.
Feed Rate Issues:
Causes: Excessive feed rates may overload the blade, while insufficient feed rates can prolong cutting time, affecting accuracy.
Solutions: Optimize feed rate settings to balance cutting efficiency and accuracy.
Coolant Issues:
Causes: Insufficient or improper use of coolant can cause blade overheating, affecting cutting accuracy.
Solutions: Ensure adequate and even coolant application, and replace coolant regularly.
3. Operational Issues
Operator skills and operational standards significantly impact cutting accuracy.
Material Clamping Issues:
Causes: Improper or inaccurate material clamping can lead to cutting deviations.
Solutions: Train operators to ensure materials are clamped securely and positioned accurately.
Program Input Issues:
Causes: Incorrect program input or improper parameter settings can result in inaccurate cutting dimensions.
Solutions: Carefully verify program parameters to ensure accurate input.
Operational Errors:
Causes: Operator mistakes may cause abnormal equipment operation, affecting accuracy.
Solutions: Strengthen operator training to ensure familiarity with equipment operation procedures.
4. Environmental Issues
Changes in the working environment can also affect cutting accuracy.
Temperature Variations:
Causes: Temperature fluctuations can cause thermal expansion or contraction of equipment components, affecting accuracy.
Solutions: Maintain stable workshop temperatures and install temperature control equipment if necessary.
Vibration Interference:
Causes: External vibrations or equipment-induced vibrations may impact cutting accuracy.
Solutions: Ensure the equipment is installed on a stable foundation and kept away from vibration sources.
5. Material Issues
The characteristics of the material itself can also influence cutting accuracy.
Uneven Material Hardness:
Causes: Uneven material hardness may cause uneven blade stress during cutting, affecting accuracy.
Solutions: Select materials with stable quality or preprocess materials before cutting.
Irregular Material Shape:
Causes: Irregular material shapes may complicate clamping, affecting cutting accuracy.
Solutions: Preprocess irregularly shaped materials to ensure stable clamping.
Inaccurate material dimensional accuracy in CNC sawing machines can result from various factors, including equipment, process, operation, environment, and materials. To address this issue, the following steps should be taken:
Regularly maintain equipment to ensure key components (such as blades, guide rails, and clamping devices) are in good condition.
Optimize cutting process parameters to ensure appropriate cutting speed, feed rate, and coolant usage.
Strengthen operator training and standardize operational procedures.
Improve the working environment to minimize the impact of temperature and vibration on equipment.
Select materials with stable quality and preprocess irregular materials.
Through systematic analysis and targeted improvements, the cutting accuracy of CNC sawing machines can be effectively enhanced, ensuring product quality and production efficiency.