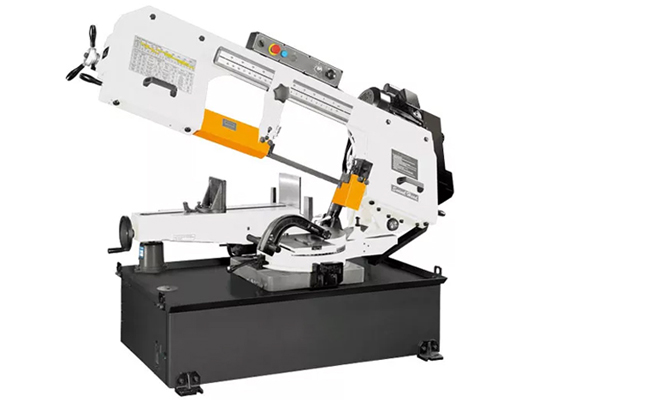
How to Prevent Band Saw Blade Breakage
To prevent band saw blade breakage, it’s essential to address equipment condition, operating procedures, blade selection, and maintenance. Here are the key measures:
1. Equipment Inspection and Adjustment
Saw Wheel Alignment
Ensure the upper and lower wheels are parallel and aligned in the same vertical plane to prevent blade twisting or side stress.
Check for wheel wear or eccentricity and replace or repair if necessary.
Guide Adjustment
Maintain proper guide block (or bearing) clearance—too tight increases friction, too loose causes blade wobble (typically 0.02–0.05mm).
Position guides as close to the workpiece as possible (usually 5–10cm).
Tension Control
Set blade tension according to the manufacturer’s specifications (use a tension gauge). Too loose causes slippage; too tight accelerates fatigue.
“Break in” new blades by running them at low speed and light load for 10–15 minutes to relieve internal stress.
2. Blade Selection and Installation
Match Blade Specifications
Select the right tooth pattern (e.g., wave set for soft materials, hook teeth for hard materials) and pitch (larger teeth for thicker stock).
Ensure blade width matches wheel diameter (narrow blades are unsuitable for large wheels).
Proper Installation
Align teeth in the cutting direction (usually pointing downward).
Ensure welded joints are smooth, without bumps or cracks, to avoid stress concentration.
3. Operating Best Practices
Optimize Cutting Parameters
Avoid excessive feed pressure (especially on hard materials). Observe chips—they should be uniform and curled; powdery chips indicate excessive feed.
Maintain appropriate cutting speed (e.g., 20–60 m/min for steel, higher for wood).
Prevent Shock Loading
Secure the workpiece firmly to avoid sudden vibration or movement.
Reduce feed speed when entering/exiting cuts to prevent abrupt stress.
Cooling and Lubrication
Use cutting fluid for metalworking to reduce heat and friction (dry cutting causes thermal fatigue).
For woodworking, regularly clean resin buildup to keep the blade clean.
4. Maintenance and Care
Regular Blade Inspection
Replace blades immediately if cracks, broken teeth, or localized wear are detected.
Check for back-edge wear (which can cause breakage).
Proper Storage
Store unused blades hanging or flat to avoid bending or deformation.
Cleaning and Rust Prevention
Clean chips and debris after cutting; apply rust inhibitor for metal blades.
5. Common Causes of Breakage & Solutions
Fatigue Fracture (smooth break): Check for excessive tension or machine vibration.
Sudden Breakage (jagged break): Caused by hard spots in material or impact—adjust feed rate.
Edge Cracking: Misaligned guides or wheel wobble creates side pressure.
The key to preventing breakage is “proper equipment + correct settings + disciplined operation.” Regular maintenance, appropriate blade selection, and adherence to best practices significantly reduce breakage risk. If breakage persists, systematically check machine precision and cutting parameters.