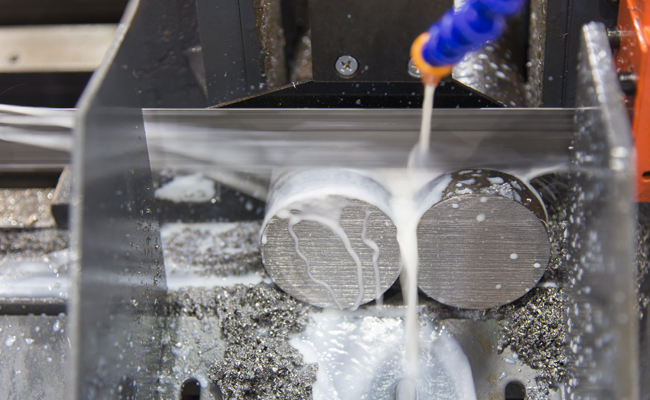
How to Choose a High-Quality CNC Sawing Machine?
Selecting a high-quality CNC sawing machine requires careful consideration of equipment performance, manufacturer reputation, after-sales service, and actual needs. Below are the key factors to help you make an informed decision:
1. Core Performance Indicators
Cutting Accuracy & Stability
Positioning accuracy (typically ≤±0.05mm) and repeatability (≤±0.02mm).
High-rigidity frame (cast iron or welded steel) with linear guides/ball screws to minimize vibration.
Cutting Efficiency
Select blade speed (e.g., 30-120 m/min for metal) based on material thickness.
Automatic feeding (e.g., servo-driven) improves batch processing efficiency.
Cutting Capacity
Maximum cutting diameter/width (e.g., circular saws for Ø600mm+, bandsaws for large profiles).
Compatibility with different materials (metal, plastic, composites) and blade types (e.g., carbide-tipped for hardened steel).
2. Key Component Quality
Control System
Brand-name CNC (e.g., Siemens, Fanuc, Syntec), supporting program storage and fault diagnostics.
User-friendly touchscreen with graphical programming.
Power System
Motor power (3-15kW typical) must match material hardness; variable speed for versatility.
Cutting Components
Bandsaws: Check blade tension control and guide arm precision.
Circular saws: Focus on spindle rigidity and blade clamping.
3. Manufacturer Evaluation
Brand & Reputation
Prefer specialized brands (e.g., Germany’s Behringer, Japan’s AMADA, Taiwan’s Saw King) and verify industry references.
Certifications
Ensure compliance with CE, ISO9001, and safety standards.
Customization
Assess ability to meet special needs (e.g., automation integration, custom fixtures).
4. Automation & Smart Features
Automation Options
Auto-loading/unloading, sorting systems (reducing labor costs).
Laser marking/vision systems (enhancing positioning accuracy).
Smart Maintenance
Blade life monitoring, adaptive cutting parameter optimization.
5. After-Sales Service & Costs
Service Network
Confirm local technical support (e.g., 24-hour on-site response).
Training and maintenance programs.
Long-Term Costs
Compare consumable (blade) prices and replacement frequency.
6. Testing & Comparison
On-Site Trials
Test cut quality (surface finish, perpendicularity).
Observe noise levels (≤75dB ideal) and chip removal efficiency.
Model Comparisons
Compare similar models across brands (e.g., hydraulic systems, safety guards).
Recommended Steps
Define Needs: Determine materials (e.g., stainless steel, aluminum), batch size, and precision requirements.
Shortlist Brands: Request proposals from 3–5 specialized manufacturers.
Factory Visits: Inspect equipment operation at production sites.
Cost-Benefit Analysis: Balance performance, price, and service—avoid low-cost compromises.