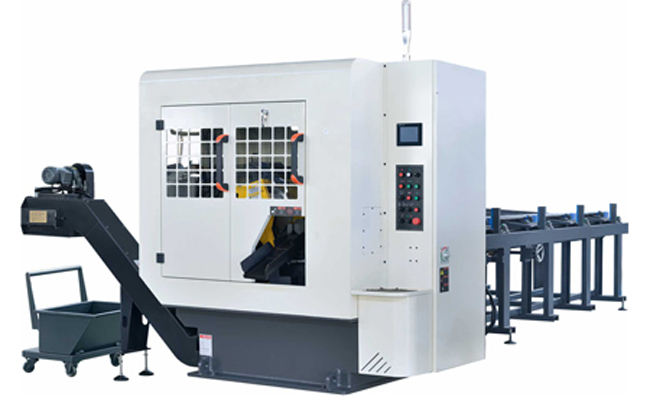
Comprehensive Guide to Band Saw Blades: Detailed Introduction and Selection
1. Basic Structure and Classification of Band Saw Blades
- Structural Composition
- Tooth Material: Determines wear resistance (e.g., high-speed steel, carbide).
- Backing Material: Provides toughness (typically spring steel or alloy steel).
- Welding Process: Affects joint strength (e.g., laser welding, electron beam welding).
- Main Types
- Bi-Metal Band Saw Blades
- Tooth Tip: High-cobalt high-speed steel (e.g., M42), wear- and heat-resistant.
- Backing Material: Flexible spring steel, fatigue-resistant.
- Applications: Stainless steel, alloy steel, titanium, and other high-hardness materials.
- Carbon Steel Band Saw Blades
- Low cost but short lifespan, prone to tooth breakage.
- Applications: Soft metals (aluminum, copper), wood, plastics.
- Carbide-Tipped Band Saw Blades
- Carbide inserts (e.g., tungsten carbide) for extreme wear resistance.
- Applications: Hardened steel, superalloys, composites.
- Diamond-Coated Band Saw Blades
- Used for ultra-hard non-metals like ceramics and fiberglass.
- Bi-Metal Band Saw Blades
2. Key Selection Parameters
- Tooth Profile
Tooth Type Characteristics Suitable Materials Regular Tooth Balanced cutting and chip removal Carbon steel, cast iron Hook Tooth Large pitch (3-6 TPI), deep gullet for fast chip clearance Aluminum, plastics, softwood Precision Tooth Fine pitch (10-14 TPI), smooth finish Thin-walled tubes, precision parts Variable Pitch Reduces vibration and noise Irregular or hollow sections - Teeth Per Inch (TPI)
- Rule of Thumb: Ensure 3-6 teeth engage the workpiece at all times.
- Recommendations:
- Soft Materials (Aluminum, Plastics): 3-6 TPI (prevents clogging).
- Medium-Hard Materials (Carbon Steel): 6-10 TPI.
- Hard Materials (Stainless Steel): 10-14 TPI (reduces load per tooth).
- Width and Thickness
- Width: Typically 6-50mm. Wider blades offer stability (ideal for straight cuts), while narrower blades suit curved cuts.
- Thickness: 0.6-1.3mm. Thicker blades resist deflection; thinner blades offer flexibility.
3. Material-Blade Matching Guide
Material Type | Recommended Blade | Tooth Profile/Pitch | Cutting Speed (m/min) |
---|---|---|---|
Low-Carbon Steel | Bi-Metal (M42 teeth) | Regular/6-8 TPI | 40-60 |
Stainless Steel 304 | Bi-Metal (high-cobalt teeth) | Precision/10-12 TPI | 20-30 |
Aluminum 6061 | Carbon Steel or Bi-Metal | Hook/3-4 TPI | 150-250 |
Titanium TC4 | Carbide-Tipped or Bi-Metal | Variable/8-10 TPI | 15-25 |
PVC Plastic | Carbon Steel Blade | Hook/2-3 TPI | 80-120 |
4. Common Issues and Solutions
- Blade Breakage
- Causes: Excessive tension, aggressive feed, worn guide wheels.
- Solution: Adjust tension to manufacturer specs (e.g., 300-400 N/mm²), inspect guides.
- Rough Cuts
- Causes: Incorrect TPI, worn blade, excessive feed rate.
- Solution: Switch to finer-pitch blade, reduce feed speed.
- Cutting Deviation (Drifting)
- Causes: Misaligned blade, unsecured workpiece, guide block misalignment.
- Solution: Re-align blade, clamp workpiece firmly, adjust guide block gap (≤0.05mm).
5. Purchasing Recommendations
- Prioritize Bi-Metal Blades: Cost-effective for 90% of metal-cutting needs.
- Carbide Blades for Extreme Hardness: Higher cost but 5-10x longer lifespan.
- Test Cuts Required: New blades need break-in (first 10 cuts at 50% normal parameters).
Top Brands:
- Industrial Grade: Lenox (USA), Bimetal (Germany), Amada (Japan).
- Budget Options: Starrett, Bahco.
6. Maintenance and Storage
- Post-Use Cleaning: Remove chips and coolant residue.
- Hang Storage: Avoid bending or pressure damage.
- Regular Inspections: Check tooth wear and weld cracks (every 8 hours).
Pro Tip: Blade life heavily depends on coolant—use dedicated fluids (e.g., emulsions for steel, pure oil for titanium).
With proper selection and maintenance, band saw blade efficiency can improve by 30% or more!
Related Posts